March 19, 2024
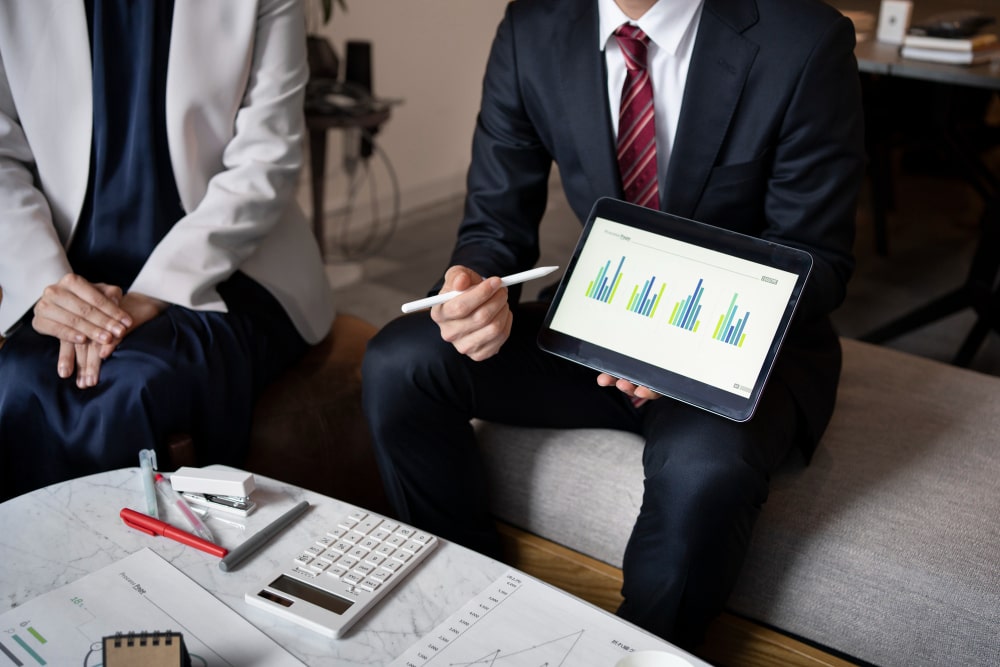
The company is involved in the manufacturing of cycles as well as components parts, chains, machines, TMT bars, steel strips etc used in the agriculture, automotive, construction and railway industries. With revenues of close to $ 1 billion, the company has recently expanded into the electric 3-wheeler, medical consumables, and mobile camera modules markets.
THE CHALLENGE
The company has 22 manufacturing plants which are located in different states. Each manufacturing plant consumes a combination of lake water, ground water and externally procured water for their machinery and factory facilities. Based on the usage, water is treated in an Effluent Treatment Plant (ETP) or a Sewage Treatment Plant (STP) which are located on the factory premises. These treatment plants bring the pH value of the water down to the required levels before the water is pumped back into the lakes. Noncompliance with the government specified pH values could result in steep fines from the Pollution Control Board and the temporary closure of the factory.
Different machines require water to be mixed with coolant oils, so that it can withstand the high temperatures and pressures for various manufacturing processes. As part of the ETP processes, this water is stored in tanks where it is cooled and separated from the coolant using sedimentation. The water is then further treated to make it safe for reuse.
The factories also require water for common areas like washrooms, canteens etc and other facilities like hard water treatment plants etc. This wastewater is treated using the STP processes to bring down the pH levels.
The company wanted to understand their overall water usage at each plant, analyze the efficiency of the ETP and STP processes and continuously track the pH value of the treated water. As a publicly listed company, they had to report various KPIs on water consumption in the Business Responsibility & Sustainability Reporting (BRSR) Core report to the Securities and Exchange Board of India (SEBI) every year.
Overall, the company needed an analytics partner to build a Business Intelligence (BI) platform to get an end-to-end view of their total water consumption, while monitoring adherence to government mandated pH values.
THE SOLUTION
The team of architects and Business Intelligence specialists from Prescience Decision Solutions, a Movate company performed an assessment of the existing sensor data collection. These smart meters measured the volume and pH levels of water, at each stage of the ETP and STP processes. Previously, this data was manually captured and submitted to the company’s users. Hence, the respective plant heads were not able to perform any trend analysis, identify patterns in consumption or irregularities in pH values etc.
As part of the initial phase of this project, the team delivered 2 dashboards for a single plant. Both dashboards provided users with a graphical month-on-month comparison of data, as well as monthly, daily, shift wise and hourly readings in tables. This dashboard format helped the plant heads understand the overall ESG performance and then drill down to analyze more specific trends and readings.
The ETP and STP Analyzer dashboard provided users with the average pH values of the ETP and STP processes across each phase of water treatment. This dashboard allowed the plant head to monitor the pH values separately and jointly for the ETP and STP processes, while tracking the plant’s performance on an on-going basis.
The Water Flow Analyzer dashboard provided users with the average consumption of water for both common areas and common devices such as evaporator pumps, water softeners etc, for each plant. This dashboard allowed the plant head to monitor the water consumption in each part of the factory, compare the water consumption of common areas against the common devices, identify discrepancies and fix issues which occurred due to malfunctions or leaks.
The different technologies used for this engagement included,
- Microsoft Power BI
- MySQL
THE IMPACT
With the new BI platform, the company is now able to get detailed insights into their water consumption at a manufacturing plant and floor level. The plant heads can easily track whether their factory is fully compliant with all government regulations on water treatment, thereby avoiding expensive shutdowns and fines by the Pollution Control Board.
The access to the new dashboards allows the company to compare the efficiency of their ETP and STP processes in each plant and find out why one performs better than the other. Based on this, the company can revamp their manufacturing processes to optimize their production and water consumption.
The company can also easily track and submit details on their water consumption KPIs in the annual BRSR Core report to the SEBI.