March 12, 2024
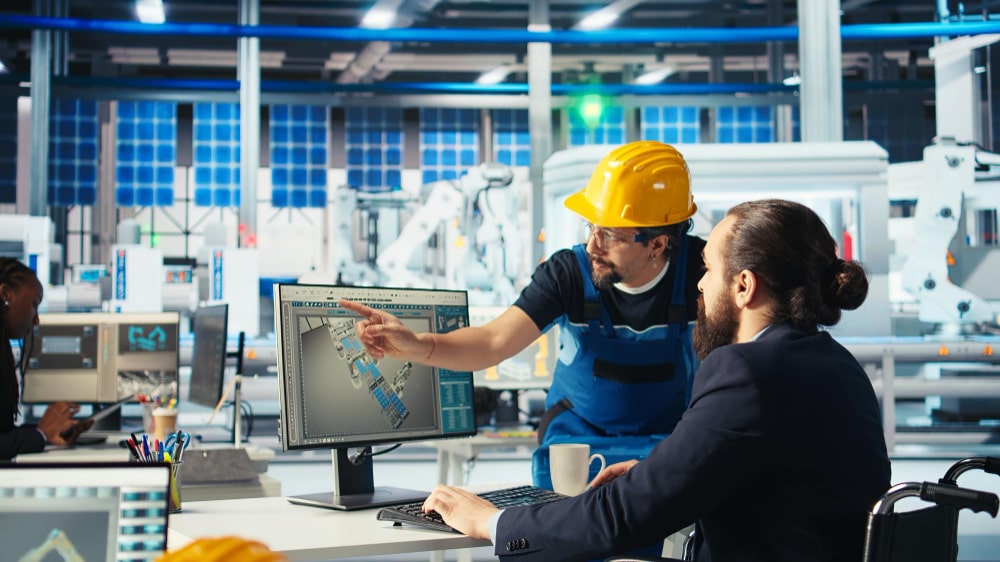
The company is involved in the manufacturing of cycles as well as components parts, chains, machines, TMT bars, steel strips etc used in the agriculture, automotive, construction and railway industries. With revenues of close to $ 1 billion, the company has recently expanded into the electric 3-wheeler, medical consumables, and mobile camera modules markets.
THE CHALLENGE
The company has more than 20 manufacturing plants across India. After raw materials, the company’s next highest operational cost is electricity, with the monthly expenditure running into hundreds of thousands of dollars. To meet the consolidated energy demands of each of its plants, the company purchases from the respective state electricity board, as well as private solar farms, wind farms and thermal power stations. The company has its own solar and wind farms also. When there are fluctuations in supply, the company resorts to using diesel generator backups, which are very expensive to run.
To optimise its electricity costs, the company needed a cost benefit analysis of ongoing manufacturing against moving it to other states where the energy costs are substantially lower. The company also wanted to understand how the monthly costs would change if they purchased more energy from the private sector, what was the increase in their costs on account of production at peak hours for electricity billing (18:00 to 22:00 IST), overall energy consumption when their machines were on load, idle or switched off, the costs incurred in using generator backups etc.
Additionally, the company wanted to measure 2 new KPIs – the output created per unit of electricity consumed and the cost of electricity per unit output created. With these new KPIs, the company could analyze the productivity of their manufacturing plants and machines.
As a publicly listed company, they had to report various KPIs on energy consumption in the Business Responsibility & Sustainability Reporting (BRSR) Core report to the Securities and Exchange Board of India (SEBI) every year.
Overall, the company needed an analytics partner to build a Business Intelligence (BI) platform to get an end-to-end view of their total electricity consumption and expenditure, based on which they could identify ways to optimize their operations, while reducing monthly energy costs.
THE SOLUTION
The team of architects and Business Intelligence specialists from Prescience Decision Solutions, a Movate company performed an assessment of the available electricity consumption data from the manufacturing plants. Previously, the company’s users only had access to an application which provided a live feed of energy readings from sensor devices that were connected to each machine.
Based on this assessment and the long-term roadmap set by the company, the Prescience, a Movate company team recommended a wide range of KPIs on
- Energy Management
- Factory Overview
- Operational Insights
- Efficiency & Savings
- Environmental Impact
The team defined the Entity–relationship model (ER model) for the BI platform. As part of the initial phase of this project, the team delivered 4 dashboards. The energy management dashboard included a month-on-month view of the company, factory, department, machine segment, and individual machine electricity consumption, including on-load versus idle versus off stage. The trend analysis dashboard provided a detailed view of each plant’s consumption including equipment against common areas etc. These two dashboards were built for the company management.
The month and daily consumption analysis dashboard was created for the plant heads. It showed the energy consumption for each plant and machine, based on the average monthly and daily slabs. If the readings were higher than expected, it automatically generated an alert.
The detailed analysis dashboard was designed for the plant managers. This showed the consumption for each plant and machine, as well as the readings from the sensor devices. If any sensor provided an abnormal reading, the plant manager immediately assigned an employee to investigate why the device was faulty or to check if it was disconnected.
The different technologies used for this engagement included,
- Microsoft Power BI
- MySQL
- Draw.IO
THE IMPACT
With the new BI platform, the company’s management, plant managers and plant heads can get detailed insights into their electricity consumption at an overall, manufacturing plant and machine level. The access to the new KPIs and analysis of charges during peak billing hours allows them to understand the cost variations in their existing manufacturing processes.
Also, the company is now able to compare the productivity of each of their plants and machines to identify why one performs better than the other. Based on this, the company can revamp their manufacturing processes to optimize their production output at reduced costs.
The company can also easily track and submit details on their energy consumption KPIs in the annual BRSR Core report to the SEBI.